A number of tools and technologies necessary for the Russian industrial sector have become unavailable because of the sanctions pressure. These include sensors for nondestructive testing used in various fields from mining to machine manufacturing and shipbuilding, as well as testing products created by 3D printing. Development of domestically-produced sensors and, in the long run, a detector for laboratory tests will be carried out in the laboratory of young scientists, Microelectronics of Multispectral Quantum Introscopy of Tomsk State University. The new division was set up at TSU after winning the competition of the Ministry of Education and Science of the Russian Federation, held as part of the national project Science and Universities.
The laboratory's focus will be the development of energy-dispersive systems for nondestructive testing of low-contrast defects in polymer composites and products made from them.
“The relevance of this initiative is the ever-developing technologies of composite materials production based on high performance polymers,” says the head of the laboratory, Pavel Kosmachev, scientist at TSU and Institute of Strength Physics and Materials Science of the Siberian Branch of Russian Academy of Sciences. “What makes them stand out is high strength/weight ratio, stiffness, and ability to withstand high temperatures. That is why they are in demand in such high-tech fields as the space and aircraft industries. At the same time, it is very important to test the structure of parts and assemblies at the production stage, where heavy thicknesses and complex reinforcement make traditional methods of nondestructive testing pretty much futile.
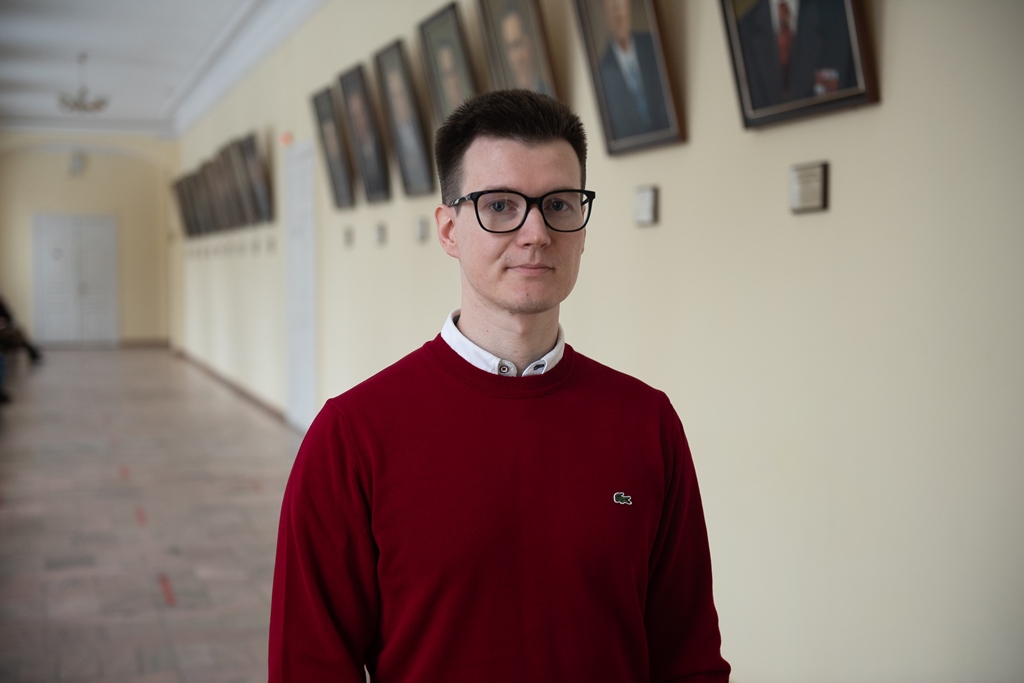
Scientist at Tomsk State University and Institute of Strength Physics and Materials Science of the Siberian Branch of Russian Academy of Sciences, Pavel Kosmachev
To solve this, energy-dispersive systems for nondestructive testing of low-contrast defects will be developed. It can be extremely difficult to detect them by an X-ray that gives a black-and-white picture. TSU-manufactured sensors will produce images in different energy spectra making it possible to detect low-contrast inclusions. Along with this, scientists will create techniques for image processing and analysis, as well as a detector for use in the laboratory.
The laboratory is entrusted with other tasks, such as the development of spectrometry sensors and spectral imaging systems for different types of radiation. Until now, Russia had not engaged in such homegrown projects since only foreign sensors were used. One of their application areas is the extractive industry. For example, spectrometers are the main analytical tool in geology and the extractive industry. In addition, such tools are necessary for quality control of products created using additive technologies.
A large scientific groundwork laid by TSU radiophysicists will be used to create new domestic sensors. An important role will be played by the data that scientists are currently receiving in the project “Development of the Fundamental Foundations of Physics and Radiation-Resistant Semiconductor Structures Technology and the Creation of Multi-Element Detectors Based on Them to Ensure the Provision of Research and Research Infrastructure of the 4th Generation Synchrotron Center SKIF and other Megascience Projects in Russia”. The research is carried out with the support of a megagrant of the Government of the Russian Federation.
“Basically, in the new laboratory we will be able to compile the scientific knowledge obtained in this project and use it in the production of applied tools and technologies for the further development of Russian microelectronics,” explains Anton Tyazhev, participant of the project and staff scientist at the TSU Laboratory of Synchrotron Radiation.
In the new laboratory created at Tomsk State University, the bet is placed on young scientists. The average age of staff is approximately 33 years. The project is designed for three years with the possibility of extension. In 2025, the university scientists will present microelectronics prototypes ready for domestic industrial implementation.