Tomsk State University materials science experts have mastered a technique that streamlines the manufacturing of metallic implants, making the whole process faster and the number of defects fewer. The scientists plan to produce titanium-nickelide implants with laser technology, which will produce personalized products using computer tomography scans.
“Currently, porous metallic implants undergo the following production cycle. First we take the intermediate component made of titanium-nickelide powder, for example. Then we use self-propagating high-temperature synthesis to get an ingot that will later on be subjected to further treatment,” explains a staff member of the TSU Laboratory of Superelastic Biointerfaces, Aleksandr Garin. “After a workpiece is finalized, we get a lot of leftover materials, plus the time expenditures can be very significant. TSU materials scientists plan to enhance implant manufacturing using direct laser deposition (DLD).”
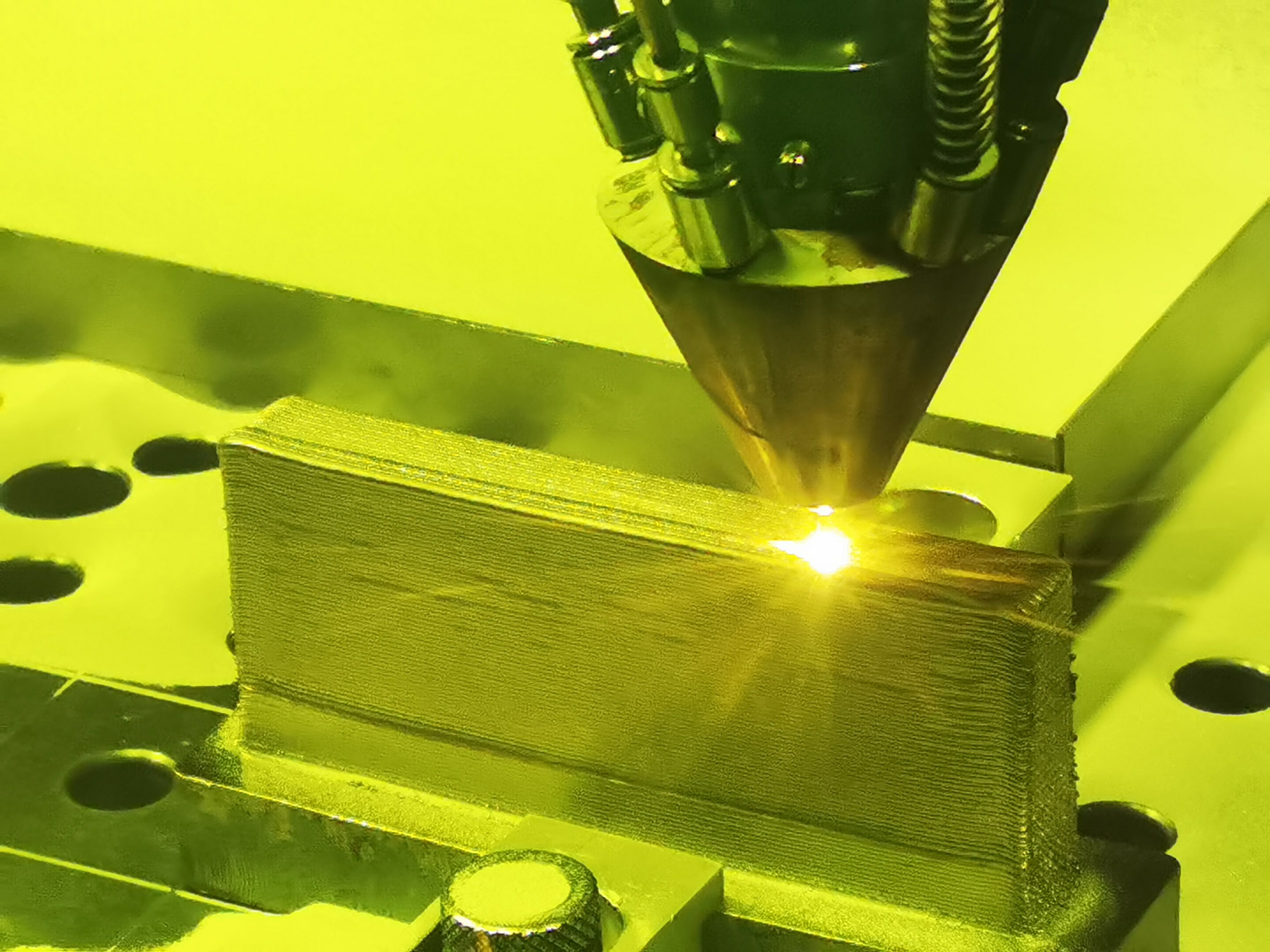
This technique is used in the aircraft, auto, and power industries as well as other fields, proving to be more promising than conventional manufacture methods. DLD enables creating complex shapes that are impossible to create relying on regular approaches such as milling or turning. Also, additive manufacturing reduces waste amounts, for the only material required is the workpiece material. Finally, the possibility of creating objects with complex inner structures makes it possible to enhance implants’ mechanical properties and reduce their weight.
TSU scientists adopted the DLD use practices from the Institute of Laser and Welding Technologies of St. Petersburg State Marine Technical University. TSU scientist Aleksandr Garin underwent training at SMTU—there he learned how to operate the university-produced equipment kit ILIST 2XL as well as the programs PowerMill and PowerShape used for modeling, simulating, and creating DLD control frameworks.
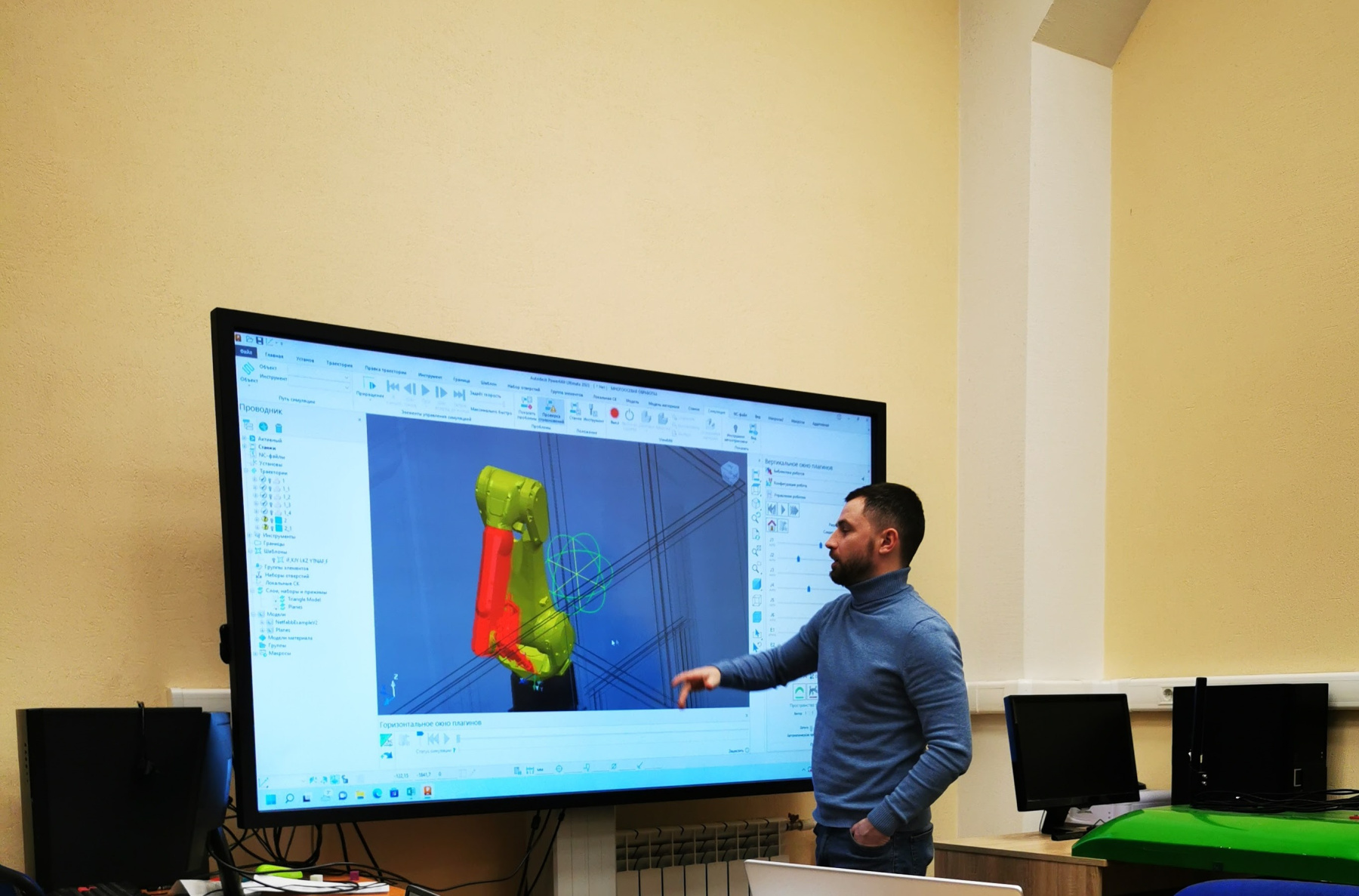
“DLD incorporates a laser beam that creates 3D objects by depositing powder layer by layer,” shares Aleksandr Garin. “We consider ILIST 2XL to be capable of creating implants, and we do believe it can be used to suit a client’s personal needs. We hope that by combining our expertise in powder metallurgy and additive manufacturing we will be able to market our technology.”
Staff scientists at the TSU Laboratory of Superelastic Biointerfaces have a wide range of expertise in implant construction for repairing hard and soft tissues (skin, muscles, blood vessel walls, sinews, inner organs). As part of a project funded by the Russian Science Foundation, TSU materials scientists conceptualized a new technology for creating composite biocoatings, which are a crucial part of human bones. The new approach reduces the chance of postoperative complications and the time it takes for titanium-nickelide implants to integrate after bone tissue replacement.
Photo and video by: Aleksandr Garin